In diesem Thema wurde viel über Federkennlinien, Federkonstanten und unterschiedliche Anzahl Federwindungen geschrieben. Das Verhalten der Feder beim Einfedern wurde diskutiert und Berechnungsmöglichkeiten aufgezeigt.
Doch wie sich die Gabelfeder der NC beim Einfedern tatsächlich verhält ist mir, ehrlich gesagt, aus den Teils konträren Aussagen nicht wirklich klar geworden. Deshalb habe ich gestern einen Versuch gemacht. Ich nahm eine Originalfeder und habe diese erst einmal vermessen.
Gesamte Feder: Länge ungespannt : 404 mm
Enge Wicklung: Länge ungespannt ca. 120 mm, Anzahl Windungen ca. 16, Abstand der Windungen ca. 2,5 mm
Weite Wicklung: Länge ungespannt ca. 294 mm, Anzahl Windungen ca. 20, Abstand der Windungen ca. 9,5 mm
Drahtstärke 5 mm
Die im weiteren aufgeführten Messwerte sind mit einer Toleranz zu betrachten, dies liegt an meinen Messmöglichkeiten, meinem Unwissen wie genau gemessen wird und dem Versuchsaufbau (dazu später genaueres).
Dann fertigte ich einen Versuchsaufbau an.
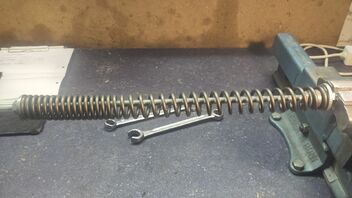
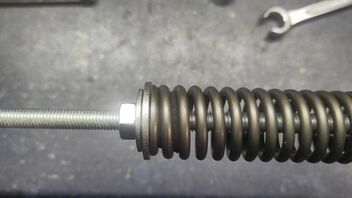
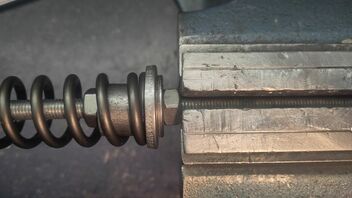
An einer 10-er Gewindestange fixierte ich zwischen zwei Muttern eine große U-Scheibe, dann noch auf einer Seite eine Hülse daran geschoben und mit einer Mutter fixiert. Nun die Feder auf die Gewindestange geschoben bis sie an der U-Scheibe anliegt und von der Hülse zentriert wird. Am anderen Ende ebenfalls eine große U-Scheibe bis an die Feder geschoben und mit einer Mutter fixiert. Die Gewindestange im Schraubstock eingespannt und dann die Mutter gedreht bis die Feder um 15 mm zusammen gedrückt ist. Dies entspricht in etwa der Vorspannung in der Gabel, um 5 mm mehr oder weniger brauchen wir jetzt und hier nicht diskutieren.
Jetzt habe ich die Feder schrittweise um 10 mm gespannt und die Abstände der Federwindungen in beiden Bereichen gemessen. Hier die Daten der Messreihe:
Federweg | Enge Wicklung (Abstand in mm) | Weite Wicklung (Abstand in mm) |
vorgespannt | 2,1 | 9,2 |
+ 10 mm | 1,8 | 8,7 |
+ 20 mm | 1,6 | 8,4 |
+ 30 mm | 1,4 | 8,1 |
+ 40 mm | 1,3 | 7,8 |
+ 50 mm | 1,0 | 7,6 |
+ 60 mm | 0,6 | 7,4 |
+ 70 mm | 0,3 | 7,1 |
+ 80 mm | Block | 6,4 |
Schwachpunkt ist, dass die Feder nicht geführt wird (in der Gabel macht dies das Standrohr) und ich keine weiteren Hülsen auf die Gewindestange gesetzt habe (hatte keine weiteren zur Verfügung). Dadurch drückt sich die Feder seitlich weg bis sie an der Gewindestange anliegt. Dabei beschreibt sie ein leichtes „S“ und das messen der Wicklungsabstände im Bereich der weiten Wicklung ist anfangs durch mehrere Messungen und Mittelwertbildung noch möglich. Bei weiterem „einfedern“ wird diese Messung jedoch immer ungenauer. Im Bereich der engen Wicklung ist dieser Effekt nicht so ausgeprägt und die Messung dürfte genauer sein.
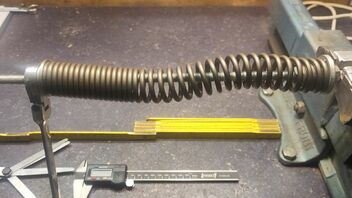
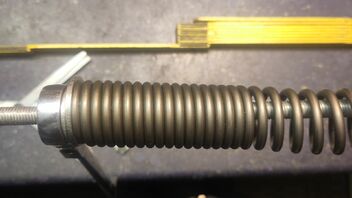
Natürlich könnte man den Versuchsaufbau verfeinern und eine neue Messreihe durchführen um damit genauere Messergebnisse zu erhalten. Das war mir aber zu langwierig, deshalb habe ich das nicht mehr gemacht. Und um den grundsätzlichen Ablauf des Einfedervorganges zu verstehen sollte auch die mit diesem Versuchsaufbau durchgeführte Messreihe ausreichen. Einige Aussagen in diesem Foren-Thema können durch meinen Versuch bestätigt werden.
Meine Interpretation der Messreihe ist folgende. Mit Beginn des Einfederns arbeiten beide Federbereiche weil auf beide eine Kraft ausgeübt wird, die Federkonstante über beide Bereiche ist niedrig. Nach rund 60 mm Federweg ist die eng gewickelte Feder auf Block. Wird weiter eingefedert arbeitet nur noch der weit gewickelte Bereich, die Federkonstante ist höher. So wird die „Progressivität“ der Feder in der Praxis konstruktiv umgesetzt.
Ich hoffe das ich alles verständlich beschrieben habe.